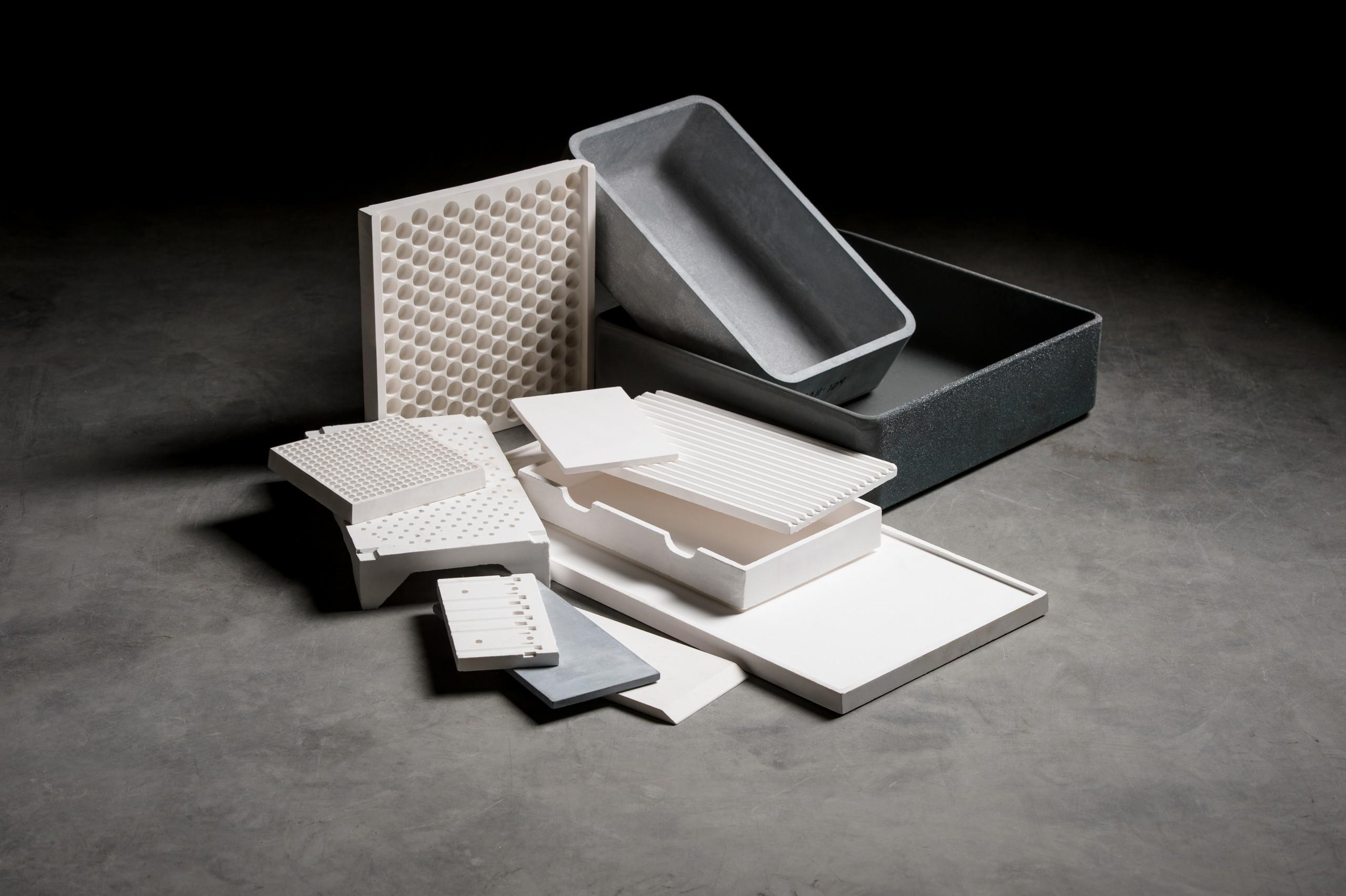
Core Setters
Blasch's unique casting process contributes to the successful application of high purity core setters for the heat treating industry. Blasch pre-cast tight tolerance shapes available with unique features unheard of in the industry coupled with several available high purity materials eliminates premature failure and the need for secondary operations. Available in a variety of premium refractory materials, these systems are individually engineered to fully support our customers’ product during de-binding and sintering.
Whether you are sintering a metal injection molded (MIM) part, a zirconia dental fixture, or calcining Lithium powders, Blasch engineers can help you design a custom setter or sagger for your specific requirements. With our unlimited design, shape, and size capability coupled with our unparalleled tolerance control, we can help you increase your throughput with existing furnaces whether they are batch or continuous.
Products like PIM/MIM Setters, airfoil core setters, PM sintering fixtures, pusher plates, saggers for calcining, sintering and heat treating are all available.
For more information or to receive a quote for these products, contact us today.
Blasch continues to aggressively expand our product offering through material development. To improve the life of ceramics used in high-temperature reducing environments, we have undertaken several projects to develop ultra-high alumina products with minimal silica, as well as MgO/Spinel based materials to address a growing need for basic materials.
Blasch engineers are constantly advancing the state of the art with regard to ceramic formulations suitable for heat-treating applications and in sophisticated manufacturing processes that produce near-net-shape ceramic parts having tight tolerances, low shrinkage, and controlled porosity and density. Knowing component or powder manufactures are being forced to increase throughout, the demand for thermal shock resistance increase as they push their furnaces faster on heating up and cool down. Knowing the Blasch materials can handle these temperature swings is reassuring to engineers and process managers as it allows them to focus on other aspects of their bottom line.
TESTING & RESEARCH
At our Blasch headquarters test lab, our team of ceramic engineers rigorously test our product to withstand the stress of thermal shock and stresses.
- Modulus of Rupture (strength testing)
- Archimedes density (density validation)
- Thermal shock resistance (rapid temperature changes)
- Creep deflection (deformation measurement)
- Corrosion resistance (oxidation resistance)
- Wear resistance (abrasion and force)
ADVANCED ENGINEERING:
Our team of design engineers use FEA (Finite Element Analysis) to analyze stresses of our material under varying temperatures and CFD (Computational Fluid Dynamics) to simulate fluid flow of liquids and gases.
CERAMIC MANUFACTURING:
Blasch's ISO 9001 quality system produces high tolerance nozzle geometry within half a percent. The patented Blasch process uses a proprietary forming method developed to produce complex featured ceramics with unique physical properties.
Related Resources
Learn how Blasch is able to achieve the ideal properties for a ceramic core setter to effectively work in the firing environment in this on-demand presentation by Larisa Balladares, including:
- Resistance to slumping and movement after repeated firing
- High tolerance capability
- The ability to make complicated geometry to match the ceramic core
Download Phil Geers and William Russell’s white paper: “Effects and Analysis of Thermal Stresses on Core Setters for Aerospace Applications". In this white paper, you can expect to learn more about where we explore part stresses in different orientations. Through FEA analysis we found the best way to orientate our part with minimal stress.
Download Phil Geers, William Russell, and Dave Bacchi’s white paper: "Improving Thermal Conditions and Reducing Process Costs for Core Setters in Aerospace and IGT Applications".