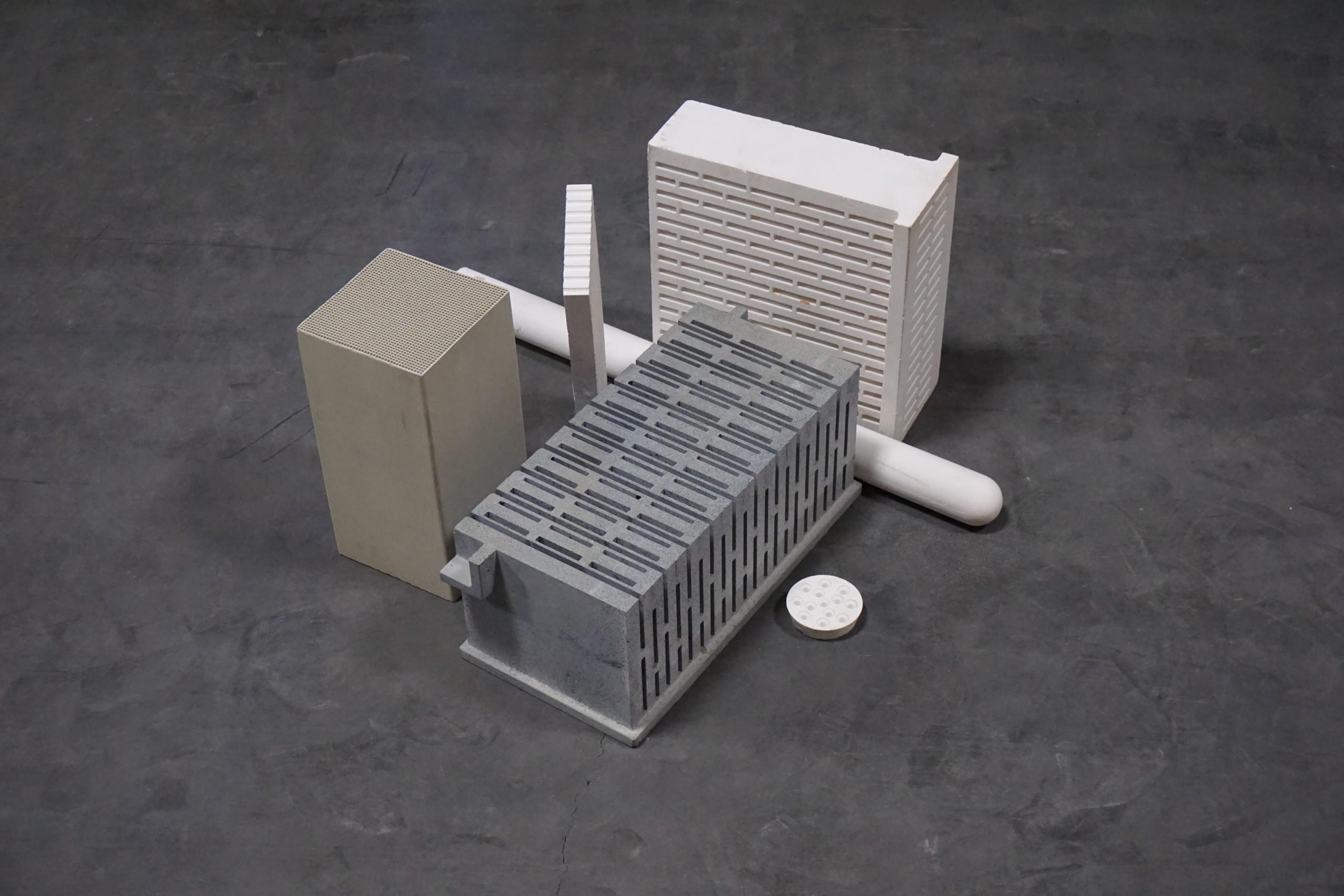
Hot Gas Filters/Candle Filters/Recuperators
Plants worldwide rely on Blasch monolithic drop-in replaceable ceramic elements specifically engineered for separating exhaust gases or recouping exhaust heat. Our cast or extruded monolithic ceramic hot gas filters can increase flows of existing hot gas scrubbers or Regenerative Thermal Oxidizers (RTOs) by reducing the media volume of new units compared to any other structured or random packing. Due to the shear surface area of monolithics, they provide the greatest available heat transfer and filter area resulting in more efficiency per unit of volume than any other type of element.
For more information or to receive a quote for these products, contact us today.
Our patented porous ceramic materials provide unique solutions for filtering exhaust gases. Blasch hot gas filters offer controlled, tight and interconnected porosity that allows gas to permeate the body. Particulate like dust, ash and POC’s are not allowed to penetrate the structure, eliminating pluggage or excessive cleaning.
FEATURES AVAILABLE FOR OUR HOT GAS FILTERS
Our hot gas filters can be configured for your specific application with:
- cast threads
- thin walls
- flanges
- ship-laps
- many other complex features
Utilizing the Blasch casting process, engineered designs maximizing filtering area and number of part numbers are achievable.
With a variety of highly chemical, abrasion and heat resistant ceramic compositions available, Blasch engineers assist both OEMs and single plants in achieving financial performance objectives by optimizing process efficiencies, reducing pressure drops, lowering energy costs, maximizing filter performance and eliminating high replacement costs traditionally found in other ceramics.